Toggle Clamp SK3-021-1
- Unit Price:US$0.64~US$0.74
- MOQ: no request
- Lead Time:7~15days
- Application:Container door; Electric box; Electric cabinet; Industrial equipment
- Features:
- Installation base divide into two parts and relatively rotating, easy to install.
- Adjustable latch rod with thread, suitable for different compression force.
- Small size with strong tightly force.
- Material:
- Cold Rolled Sheet(SPCC) or Stainless Steel(SUS304)
- Finish:
- Zinc Plated or Vibration Grinding
- Remark:
- Suitable for left and right side latching
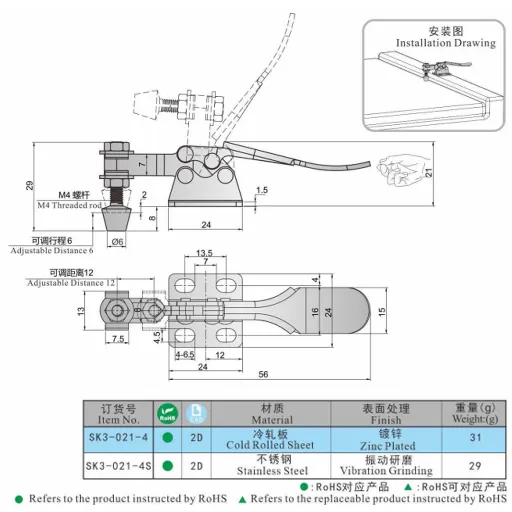
Contact Us
Need a quick response? Reach out now and our team will get back to you within 12 hours.
Tel.:
86-769-22687696
Mob.:
0086 18024916751
Fax:
86-769-22687694